
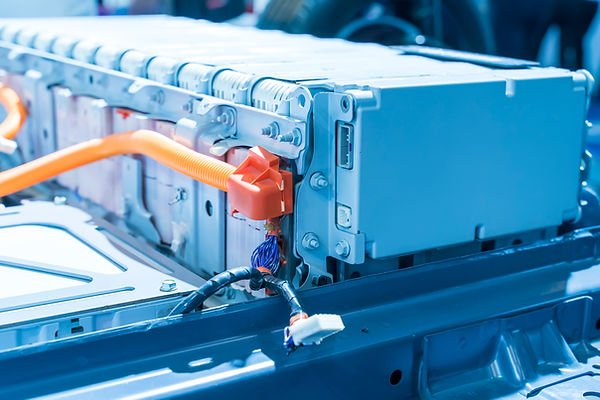
It Is Time to Go LFP
LFP chemistries provide exceptional benefits, including a long cycle life, rapid charging, and excellent safety performance.
Growing LFP Demand
Growing LFP battery market
-
The Lithium-ion battery market in the US has grown significantly in recent years and is projected to continue growing at a 19% CAGR through 2030, with Nickel Manganese Cobalt (NMC) cathode material chemistries dominating the market.
-
The US LFP cell market is emerging and has three primary end markets: Electric Vehicles (EV), Energy Storage Solutions (ESS), and Consumer Electronics.
-
The adoption of LFP cells in the US is expected to increase at a CAGR of 29% to reach a Total Addressable Market (TAM) of 291 GWh and nearly $12B by 2030.
-
This growth will be primarily driven by increasing sales of EVs and growth in ESS (63% and 42%, respectively), as LFP becomes more favorable.
LFP cathode material production
-
The production capacity of LFP cathode material in the US is currently very limited, but several companies have expressed plans to expand capacity in the coming years. The first specific commercial operating capacity for LFP cathode material is scheduled for 2024 by ICL.
-
There is still a considerable gap between the domestic scale and the demand for LFP cathode material in the US.
-
​New players include large, vertically integrated international companies with experience in LFP material production in China.
LFP
LFP is an essential element of the growing lithium-ion battery market and is considered a sustainable, cost-effective, and safe option. Primarily used in Energy Storage Systems and electric buses, a rapidly growing portion of LFP cells are now used in Electric Vehicles.
Strength of LFP
​LFP batteries are less expensive than NCA and NCM, and are an excellent cobalt-free option. Additionally, LFP batteries offer high-cycle life, fast charging, and excellent safety.
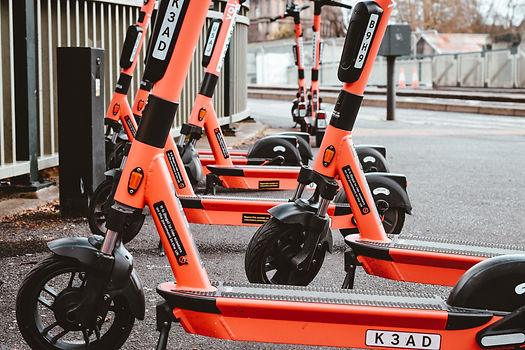
How LFP Produced?
LFP is produced from Iron Phosphate (FP), which itself is a product of phosphoric acid and iron sulfate. FP then reacts with lithium-rich compounds via pyrolysis to synthesize LFP. This specific production process for LFP is relatively power-intensive, and must be sourced from a clean energy source to meet the automotive industry's Environmental, Social, and Governance (ESG) requirements.
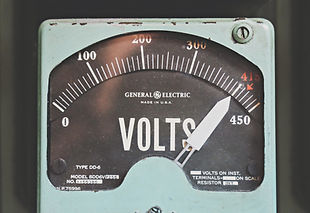
Who owns LFP battery patents?
China has been an early adopter of LFP battery technology and currently produces 95% of the world's LFP batteries. However, as key patents are set to expire soon, other countries are expected to ramp up their production. Tesla has also announced its plans to adopt LFP batteries in its standard-range vehicles worldwide and localize battery production to be closer to its factories.
LFP Market
-
According to industry projections, LFP is expected to become the dominant battery chemistry over nickel manganese cobalt (NMC) by 2028, in a global market where demand is expected to exceed 3,000GWh by 2030. Currently 90% of the world’s battery manufacturing is in the Asia-Pacific region, and this share is expected to decrease to 69% by 2030, as Europe begins to ramp up production to a projected 20%. During this period, the global LFP battery market is expected to grow from $10.12 billion in 2021 to $49.96 billion by 2028 at a CAGR of 25.6%.
Is LFP safer than NMC?
​While NMC chemistries are known for higher energy density and power capabilities, LFP based batteries are known for its safety, longer lifespan, and cost-effectiveness.
LFP Production Process
The solid phase synthesis method is a straightforward and easily scalable process for producing LFP, making it an attractive option for the large-scale manufacturing of electrode materials.
One commonly used technique for LFP production is the carbothermic reduction method, which involves improving iron purity while simultaneously coating lithium iron phosphate with pyrolytic carbon to improve conductivity.
